Coffee production from farm to cup involves a supply chain of processes that play an important part in the final quality. Dry milling is that very last process before getting those beautiful green coffee beans ready to roast.
Today we are going to take you through the 7 crucial steps involved during the dry milling process at Dinamica’s Beneficio Las Cruces so you can have a deeper understanding on what it takes to get that uniform batch of green beans that match the desired flavour profile you want in your cup.

First of all, What is a Dry Mill?
A dry mill is the place that exporters use at origin in order to clean, hull, sort and grade coffee lots according to the customer needs. At Dinamica this is the place where all the coffee arrives from our partner farms in order to be processed, packed and ready to be exported.
At Dinamica we ensure that every lot meets the quality and grading standards according to the SCA green coffee grading protocols. For this, we count on our SCA certified lab which is crucial for the reception of the lots that will be processed at the dry mill. This is where we receive the initial sample that is analysed by our team and is where the preparation of each lot is agreed according to our clients specifications.
These verifications prior to processing any coffee guarantees that the physical and sensory quality correspond to the initial quality presented by the producer. For instance, when processing microlots, we can’t accept a coffee that will be out of the physical or sensory standards if the general sample does not meet the requirements.
Without further ado, let’s go through the stages of dry milling at our Dinamica warehouse!
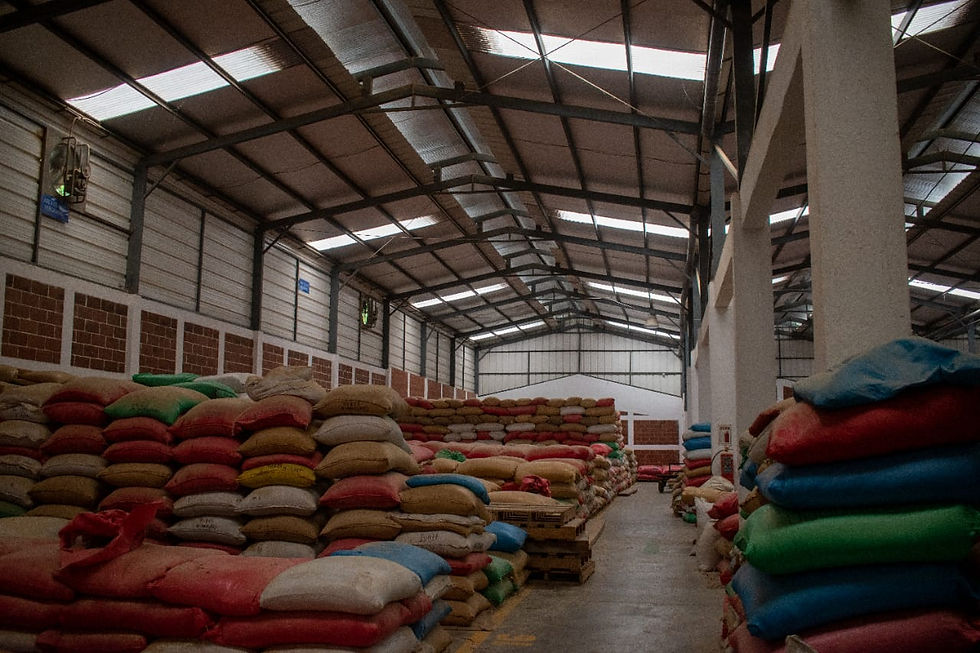
1. Sampling Reception
Sampling lots is crucial to start the milling process. At Dinamica we follow the SCA green bean grading protocols. This is how we define how the coffee will be processed from cleaning to hulling, defects sorting and bagging according to the preparation, such as American Preparation, European Preparation or Japanese Preparation, (Stay tuned for our article about Green Bean Grading!). Bean grading helps us to identify defects and faults that may require some additional steps at the dry mill.
For this, we take an homogeneous sample of 350 grs from the entire lot upon arrival of the coffee. This sample represents the physical and sensory quality of the coffee and is validated in our lab. Our quality control director Peter Engelhardt is in charge of sample milling, screening, sorting and cupping the sample and based on his diagnosis and approval the coffee lot starts the milling and preparation process.
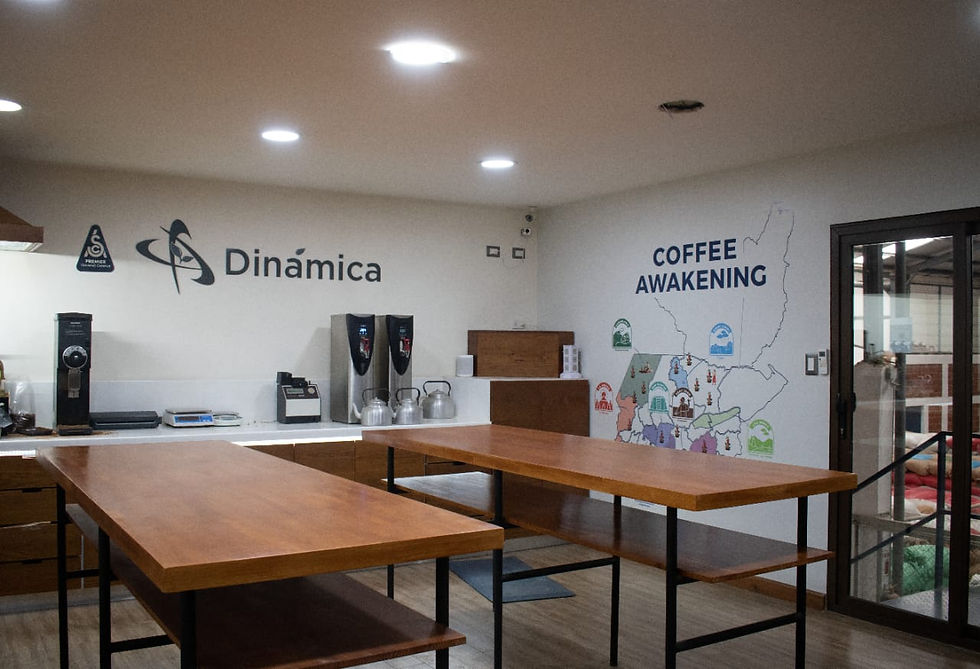
2. Destoner & Pre Cleaner
Once the lot is approved to start the milling process the sacs of parchment coffee go through the first step: Destoner and Pre Cleaner. This step is crucial to remove any foreign material such as screws, stones and sticks etc. It’s funny all the things you can get from these cleaners and that’s why they are so important! At Dinamica we use Pinhalense machines to do this work. The Pre Cleaner has the capacity to process 15,000 lbs. per hour of parchment coffee and the Destoner has the capacity to process 14,000 lbs. of parchment coffee per hour.
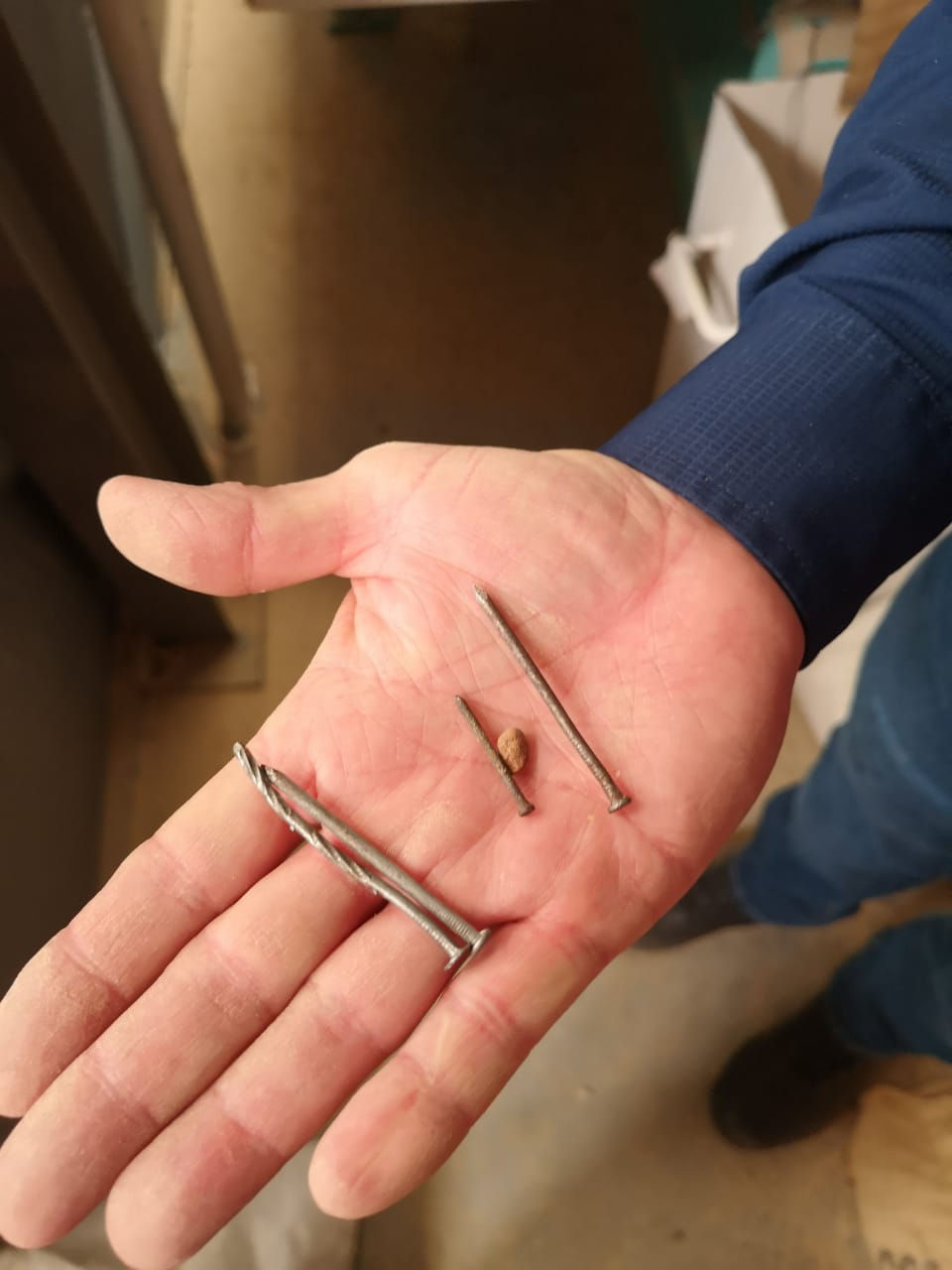
3. Dehuller
After the parchment coffee is cleaned and destoned the dehulling process takes place. This is the step where the husk is removed from the beans giving us as a result cleaned green beans ready to be sorted. Our Dehuller has the capacity to process 125,000 lbs. of parchment coffee per hour.
At Dinamica we process microlots from 60 kg to 60 bags of 69kg of parchment coffee in a special dehuller for microlots with the capacity to process 1,200 lbs. per hour.

4. Screen Sorter / Size Grader
This machine is composed of 5 sieves or layered screens each one with holes of different diameters which are numbered from 13 to 17 and are in charge of separating the beans by size. For microlots we select the beans that are classified in the sieve number 15 and upwards. Regarding the remaining beans in the sieve 14 and 13, these are used for other orders with different quality specifications.
Our screen sorter has the capacity of processing 13,000 lbs. of cleaned coffee per hour.

5. Density Sorter / Densimetric Beds
We now have green beans already classified by size that need to go through three different density sorters or densimetric beds. A density sorter is a machine known as a gravity separator that shakes the sized beans on a tilted table, so the heaviest and densest beans vibrate to one side of the pulsating table, and the lightest to the other side in order to get an homogeneous mass at the end of the process getting only the densest beans..
Our Density Sorter has the capacity to sort 8,000 lbs. of green beans per hour.
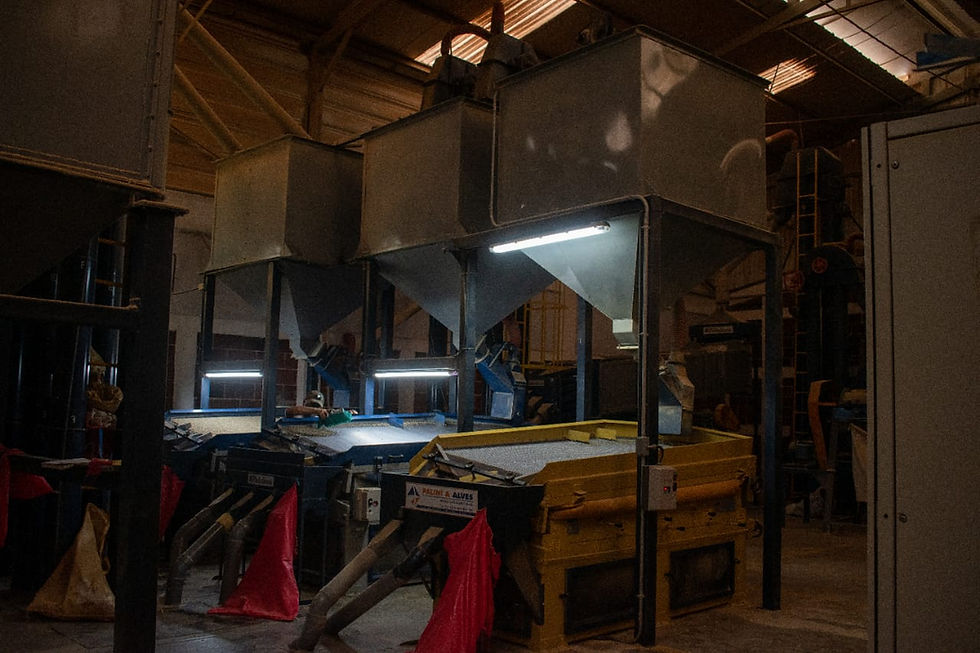
6. Color Sorter / Eye Sorter
We are now approaching the last step of selection with the color sorter. This is where some color beans such as red, white, yellow and black are taken out from the mass through a Bühler Eye Sorter machine that is programmed with the parameters of color that need to be removed. It is a stream of beans that fall fast and continuously while the sensors remove the color beans according to the parameters with a puff of air that takes the bean out of the stream. This allows us to avoid hand sorting as a way to be more efficient and precise with our selection.
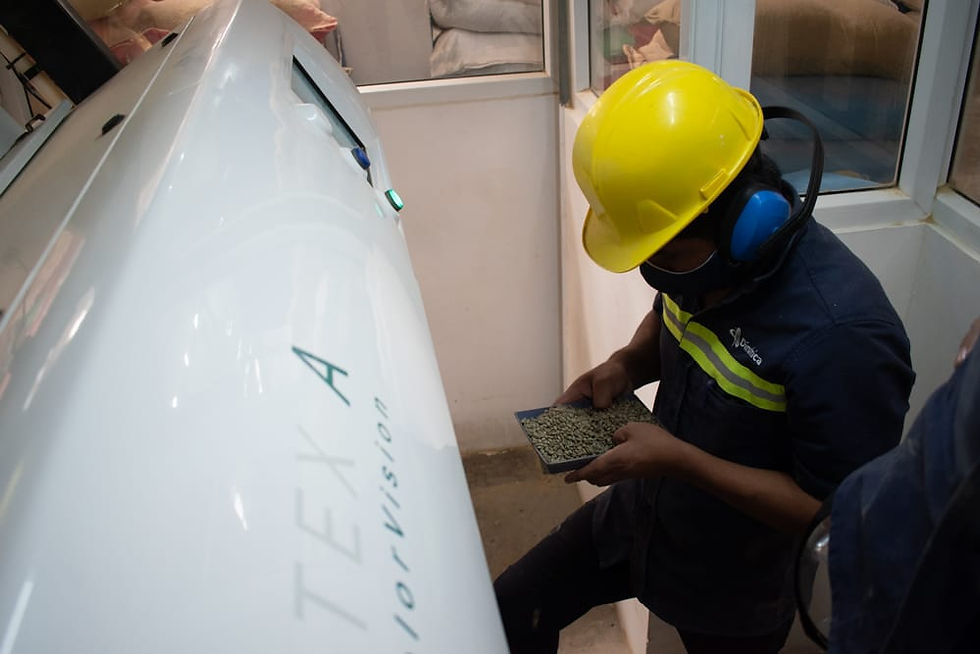
7. Bagging
Once the beans are dehulled, cleaned and sorted these go to the Final Product Silo that does the bagging of the beans in 69 kg bags of green beans that will be ready to export. Then the bags are piled in the warehouse with their respective codes waiting for their turn to reach our clients’ roasteries!
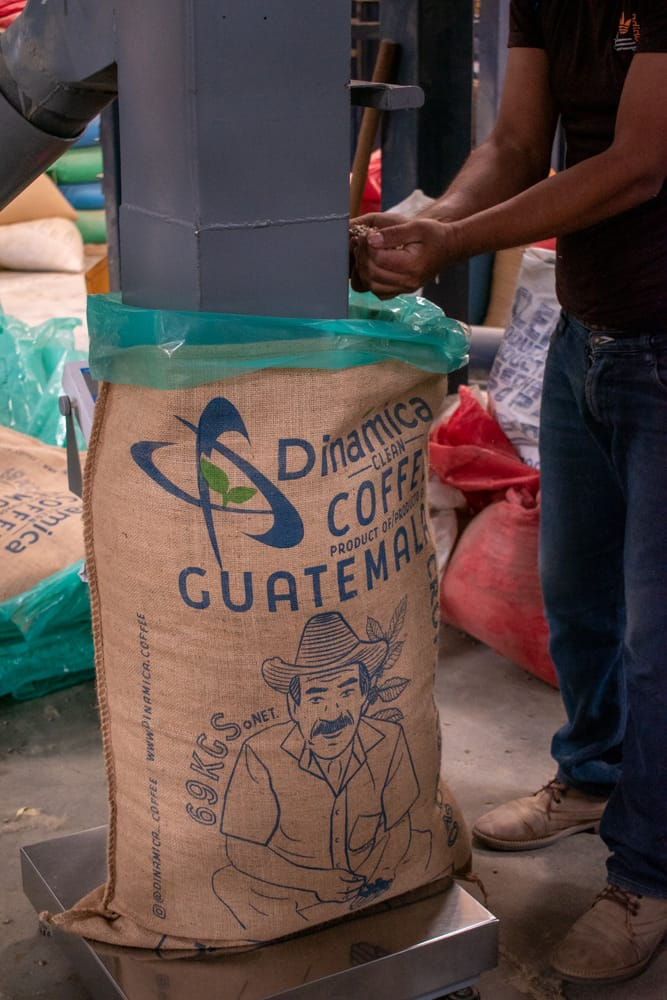
Dry milling along with green coffee export are super interesting processes. Many people are involved and many people get the benefits from it. We are thrilled to be able to work in this very last part of the chain responsible for preparing and taking care of these beans that have been produced and brought to us with so much dedication.
Comments